In the realm of filling technologies, magnetic drive pump filling stands out for its sealless and safe design. Let’s delve into the science that makes this technology so revolutionary.
The core principle of magnetic drive pump filling lies in the use of magnetic fields to transfer torque and power. Instead of traditional mechanical seals, which are prone to leaks and wear, magnetic coupling ensures a hermetically sealed connection between the motor and the pump. This eliminates the risk of leakage, making the filling process highly reliable and contamination-free.
The absence of seals also contributes to enhanced safety. Without potential leak points, there is a reduced chance of hazardous substances escaping, especially in applications involving flammable, toxic, or corrosive liquids. This makes magnetic drive pump filling ideal for industries where safety is of the utmost importance, such as chemical processing and pharmaceuticals.
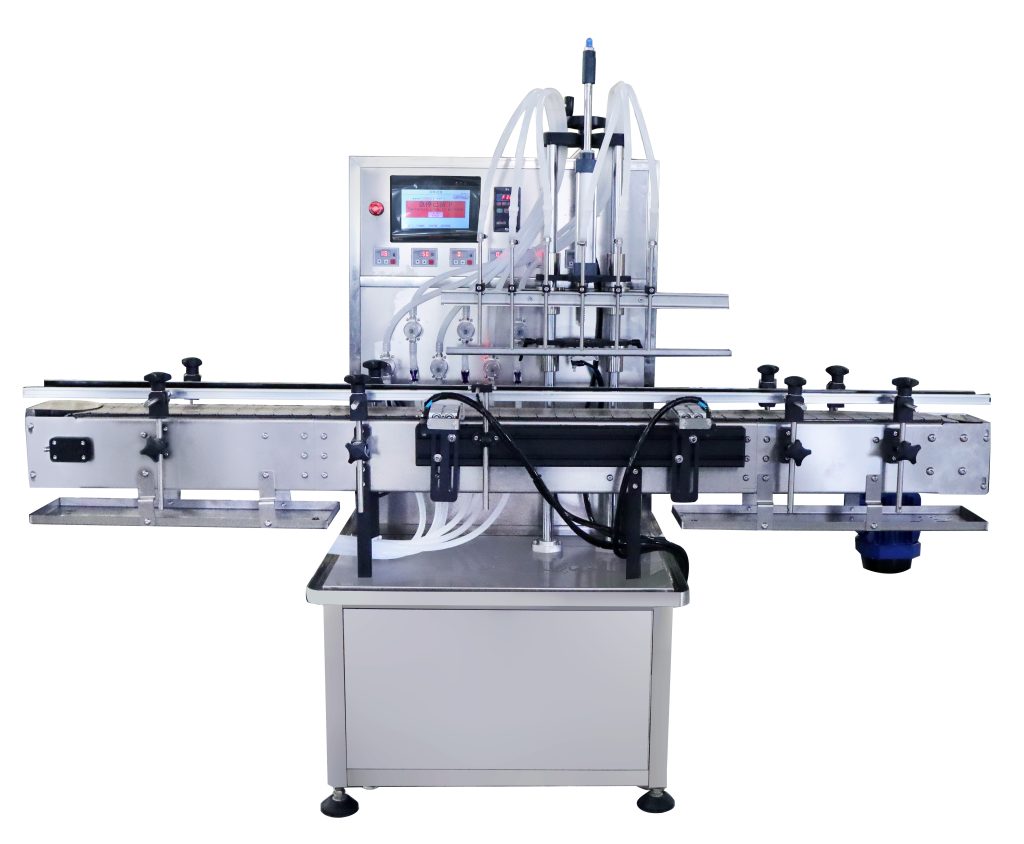
The science behind the magnetic coupling allows for precise control and regulation of the filling flow rate. Sophisticated control systems ensure that the liquid is delivered accurately and consistently, minimizing variations and maximizing filling accuracy.
The materials used in the construction of magnetic drive pumps are carefully selected to withstand the demands of different liquids and operating conditions. Corrosion-resistant alloys and high-quality polymers ensure long-term durability and performance.
The design also incorporates efficient energy transfer mechanisms, reducing power consumption and operating costs. This not only makes the technology environmentally friendly but also economically viable for businesses.
In summary, the science of magnetic drive pump filling technology combines sealless operation, safety, precision, and efficiency. It provides a cutting-edge solution for filling applications, offering peace of mind and superior performance in a wide range of industries.