In the dynamic landscape of the milk powder industry, packaging plays a pivotal role in maintaining product quality, ensuring safety, and appealing to consumers. Enter the fully automatic milk powder vacuum nitrogen flushing seaming machine—a revolutionary piece of equipment that is set to redefine the standards of milk powder packaging.
Table of Contents
The Imperative of Advanced Packaging in the Milk Powder Sector
Milk powder is a highly nutritious product that is sensitive to environmental factors. Exposure to oxygen, moisture, and light can lead to a cascade of negative effects. Oxidation can cause the breakdown of essential nutrients like vitamins and fatty acids, resulting in a loss of nutritional value. Moisture can lead to clumping, making the milk powder less appealing and difficult to dissolve. Moreover, these factors can also promote the growth of microorganisms, posing a risk to consumer health.
Traditional packaging methods often struggle to provide an adequate barrier against these elements. Manual or semi – automatic processes may not be able to achieve a consistent and airtight seal, leaving the milk powder vulnerable to spoilage. This is where the fully automatic milk powder vacuum nitrogen flushing seaming machine steps in as a game – changer.
How the Machine Operates
Vacuum Creation
The first stage of the process involves creating a vacuum within the packaging container. As the milk powder – filled container enters the machine, a powerful vacuum pump is activated. This pump rapidly removes the air from the container, reducing the oxygen level to a minimum. By eliminating oxygen, the machine effectively slows down the oxidation process, preserving the freshness and nutritional content of the milk powder.
Nitrogen Flushing
Once the vacuum is established, the machine fills the container with nitrogen gas. Nitrogen is an inert gas that does not react with the milk powder. It displaces any remaining oxygen and creates a protective atmosphere inside the container. This nitrogen – rich environment acts as a shield, preventing the milk powder from coming into contact with oxygen and moisture. Additionally, nitrogen helps to maintain the shape of the packaging, preventing it from collapsing under the vacuum.
Precise Seaming
After the nitrogen flushing, the machine proceeds to the seaming stage. Using advanced sensors and precision engineering, the machine accurately places the lid on the container and seals it with a tight, air – tight seam. The seaming process is designed to be consistent and reliable, ensuring that every package is properly sealed to protect the milk powder during storage and transportation.
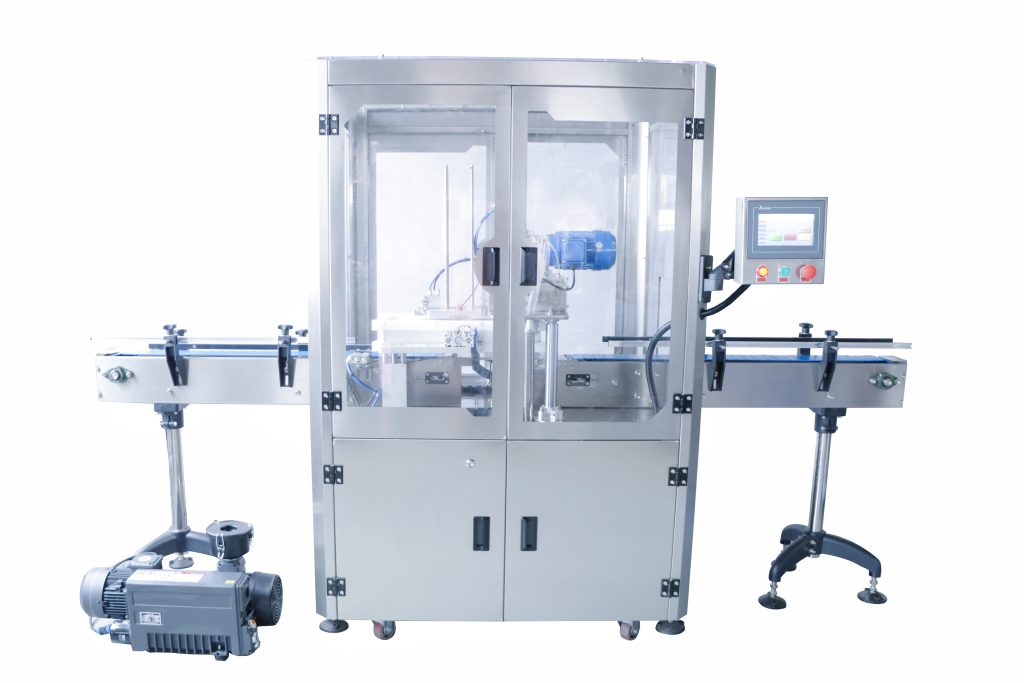
Advantages for Milk Powder Producers
Prolonged Shelf Life
The most significant benefit of using this machine is the extended shelf life it offers for milk powder. With the reduced oxygen and moisture levels inside the package, the milk powder can remain fresh and usable for a much longer time. This is a huge advantage for producers as it allows them to store their products for longer periods without worrying about spoilage. It also enables them to expand their market reach by exporting to distant locations.
Superior Product Quality
The machine helps to maintain the high – quality standards of milk powder. By preventing oxidation and moisture absorption, it preserves the original flavor, color, and nutritional value of the product. Consumers can enjoy a consistently high – quality milk powder experience, which can lead to increased brand loyalty and positive word – of – mouth.
Increased Production Efficiency
The fully automatic nature of the machine means that it can operate at a high speed with minimal human intervention. It can handle a large number of packaging units in a short period, significantly increasing the production output. This not only reduces labor costs but also allows producers to meet the growing demand for milk powder in the market.
Cost – Effectiveness
Although the initial investment in the machine may be significant, the long – term cost savings are substantial. The reduced spoilage rate means less product waste, and the increased production efficiency leads to lower unit costs. Additionally, the improved product quality can command a higher price in the market, resulting in increased profitability for producers.
Conclusion
The fully automatic milk powder vacuum nitrogen flushing seaming machine is truly a game – changer in the milk powder industry. Its innovative technology addresses the critical challenges of traditional packaging methods, offering a comprehensive solution for preserving product quality, extending shelf life, and increasing production efficiency. As the demand for high – quality milk powder continues to rise, this machine will undoubtedly become an essential tool for milk powder producers looking to stay ahead in the competitive market.