Inhoudsopgave
Introduction
In the dynamic landscape of industrial manufacturing, the process of liquid filling is a crucial operation. It impacts the efficiency of production lines, the quality of products, and ultimately, the bottom – line of businesses. Double head rotor pump filling machines have emerged as a powerful solution, capable of transforming the liquid – filling process. This article will delve into the features, advantages, and real – world applications of these remarkable machines, showing how they can unleash their full potential in various industries.
Understanding Double Head Rotor Pump Filling Machines
A double head rotor pump filling machine is a sophisticated piece of equipment engineered to fill a wide range of liquids into containers. The “double head” aspect refers to the presence of two filling heads that work in tandem. This setup allows for simultaneous filling of two containers, effectively doubling the filling speed compared to single – head machines.
The core of the machine is the rotor pump. Rotor pumps are positive – displacement pumps that use rotating elements to move the liquid. They operate by creating a sealed chamber between the rotors and the pump housing. As the rotors turn, the liquid is drawn into the chamber at the inlet and then forced out at the outlet. This mechanism enables precise control over the flow rate and volume of the liquid being dispensed.
Key Features
High – Speed Filling
The most prominent feature of double head rotor pump filling machines is their ability to fill containers at a rapid pace. With two filling heads working simultaneously, the throughput of the machine is significantly increased. For example, in a beverage production plant, a double head machine can fill hundreds of bottles per minute, ensuring that large – scale orders can be fulfilled in a timely manner.
Precise Volume Control
The rotor pump technology provides excellent control over the volume of liquid dispensed. The machine can be programmed to fill containers with a high degree of accuracy, down to a few milliliters. This is essential in industries where product consistency is key, such as the pharmaceutical and cosmetic sectors. In pharmaceutical manufacturing, accurate dosing of medications is critical for patient safety and the effectiveness of the treatment.
Compatibility with Different Liquids
These machines are highly versatile and can handle a wide variety of liquids, regardless of their viscosity. Whether it’s thin liquids like water or alcohol, or thick substances like honey, yogurt, or glue, the double head rotor pump filling machine can adapt. The pump’s design allows it to handle different flow characteristics, making it suitable for diverse applications.
Adjustable Filling Parameters
Operators can easily adjust various filling parameters, such as filling speed, filling volume, and the number of containers to be filled. This flexibility makes the machine adaptable to different production requirements. For instance, if a company is producing a new product with a different container size or filling volume, the machine can be quickly reconfigured without significant downtime.
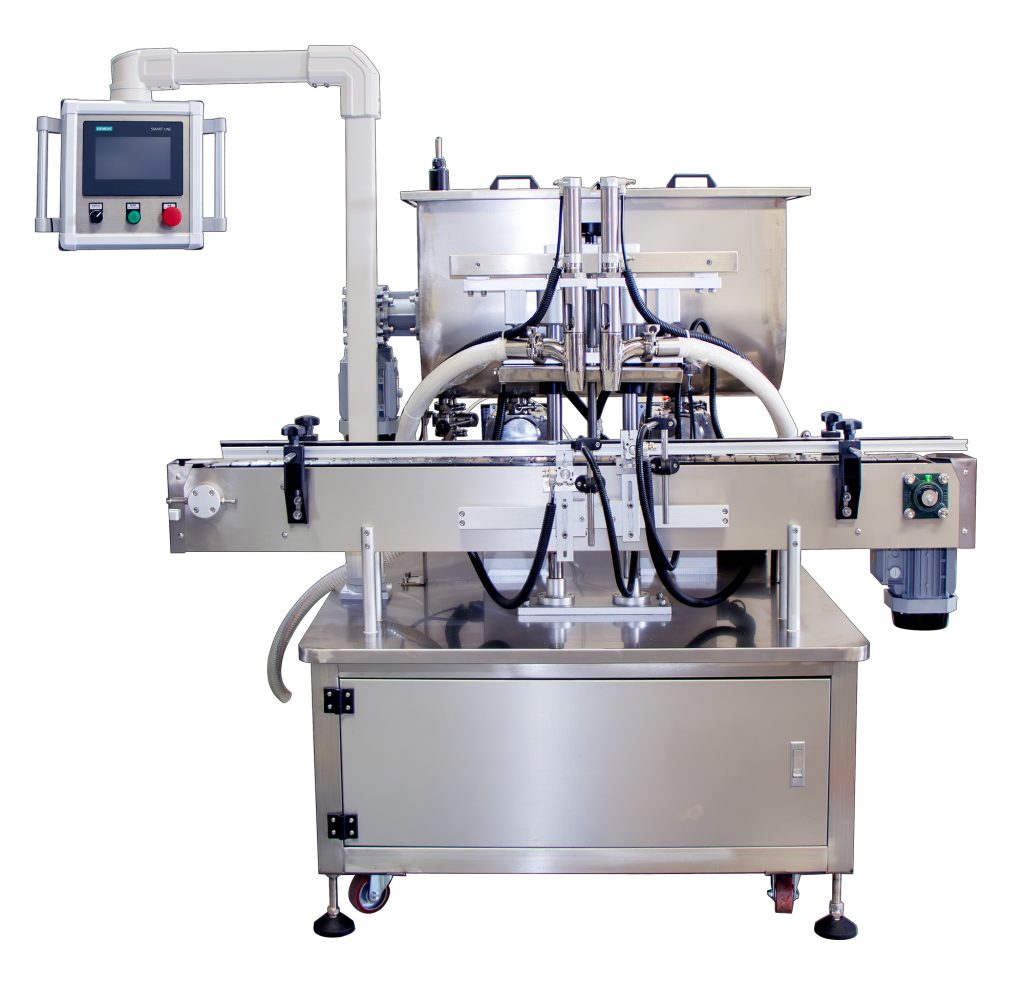
Advantages
Enhanced Productivity
The high – speed filling capability of double head rotor pump filling machines directly translates into increased productivity. By filling two containers at once, the machine can significantly reduce the time required to fill a large number of containers. This allows manufacturers to produce more products in less time, meeting market demands more efficiently and potentially increasing their market share.
Cost – Efficiency
In addition to increased productivity, these machines offer cost – saving benefits. The precise volume control reduces product waste, as there is less over – filling or spillage. This saves on the cost of the product itself. Moreover, the durability and reliability of the machine mean lower maintenance costs over its lifespan. Fewer breakdowns and less frequent replacement of parts contribute to overall cost – efficiency.
Improved Product Quality
Accurate filling ensures that each container contains the correct amount of liquid, which is crucial for maintaining product quality and consistency. In the food and beverage industry, for example, consistent filling volumes are necessary to meet consumer expectations and regulatory requirements. A double head rotor pump filling machine helps manufacturers achieve this level of quality control.
Real – World Applications
Food and Beverage Industry
In the food and beverage sector, double head rotor pump filling machines are used to fill products such as fruit juices, soft drinks, sauces, and dairy products. The ability to handle different viscosities and provide precise filling makes them ideal for this industry. They can also be integrated into existing production lines, allowing for seamless operation.
Pharmaceutical Industry
Pharmaceutical companies rely on these machines to fill medications, syrups, and creams. The high level of accuracy and hygiene standards of the double head rotor pump filling machines are essential in this highly regulated industry. The machines can be designed to meet strict pharmaceutical requirements, ensuring the safety and efficacy of the products.
Cosmetics Industry
For cosmetics like lotions, shampoos, and perfumes, the machine’s ability to provide accurate filling and handle different container sizes is invaluable. It helps cosmetic manufacturers maintain product quality and consistency, which is crucial for brand reputation.
Chemical Industry
In the chemical industry, double head rotor pump filling machines are used to fill various chemicals, solvents, and lubricants. The machines’ ability to handle different types of liquids and provide precise filling ensures the safety and quality of the chemical products.
Conclusion
Double head rotor pump filling machines are a powerful tool in the world of liquid filling. Their high – speed operation, precise volume control, versatility, and cost – efficiency make them suitable for a wide range of industries. By unleashing the power of these machines, manufacturers can enhance their productivity, improve product quality, and gain a competitive edge in the market. As technology continues to evolve, we can expect these machines to become even more advanced and efficient, further revolutionizing the liquid – filling process.