Table of Contents
Introduction
In the jam – making industry, the process of capping glass jars is a critical step that directly impacts product quality, shelf – life, and consumer satisfaction. A fully automatic jam glass jar vacuum capping machine is a remarkable piece of equipment that has transformed this process. This comprehensive guide will delve into every aspect of these machines, from their working principles to their benefits and maintenance.
Working Principles of the Machine
1. Jar Feeding System
The journey of a jam – filled glass jar through the capping machine starts with the jar feeding system. This system is designed to pick up individual jars from a storage area or conveyor and place them precisely in the capping position. It can use various mechanisms such as mechanical arms, belts, or rollers to ensure a smooth and consistent flow of jars. Some advanced machines are capable of handling different jar sizes and shapes, thanks to adjustable guides and sensors that detect the jar’s dimensions and adjust the feeding process accordingly.
2. Vacuum Creation
Once the jar is in position, the machine begins the vacuum – creation process. A vacuum pump is used to remove the air from inside the jar. This is crucial for several reasons. Firstly, it helps to preserve the jam by preventing oxidation, which can lead to color changes, flavor degradation, and the growth of spoilage organisms. Secondly, a vacuum – sealed jar provides a better seal, reducing the risk of leakage during transportation and storage. The vacuum level can be precisely controlled, depending on the type of jam and the requirements of the packaging.
3. Cap Placement
After the vacuum is created, the cap is placed on top of the jar. The cap – placement mechanism is highly accurate, ensuring that the cap is centered on the jar opening. Caps can be fed into the machine through a hopper or a conveyor system. The machine uses sensors and mechanical devices to pick up the caps one by one and place them gently on the jars. Some machines are also equipped with cap – orientation sensors to ensure that the caps are placed in the correct position, especially if they have specific markings or designs.
4. Sealing Process
The final step is the sealing process. There are different methods of sealing, depending on the type of cap and the machine design. One common method is heat – sealing, where the cap is heated to a specific temperature, causing it to melt slightly and bond with the jar’s rim. Another method is pressure – sealing, where a high – pressure force is applied to the cap to create a tight seal. The machine is programmed to apply the right amount of heat or pressure for the specific cap – jar combination, ensuring a secure and long – lasting seal.
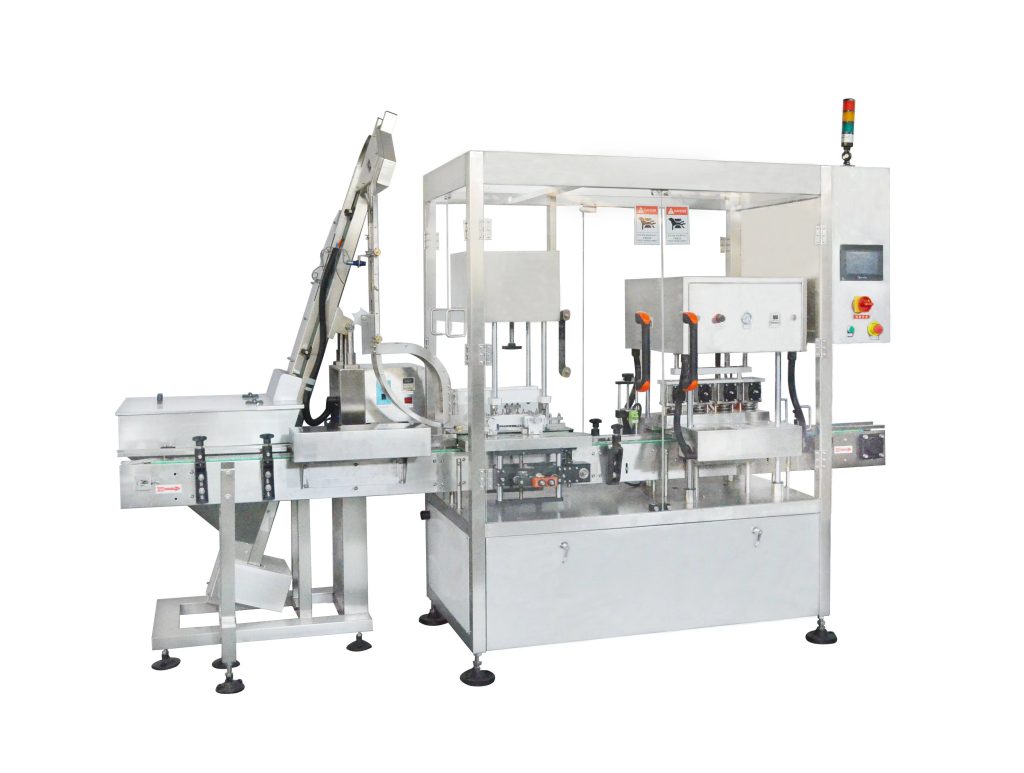
Benefits of Using a Fully Automatic Jam Glass Jar Vacuum Capping Machine
1. Increased Productivity
These machines are designed for high – speed operation. They can cap a large number of jars in a short period, significantly increasing the production output. For example, a fully automatic machine can cap hundreds of jars per minute, compared to manual capping, which is much slower and more labor – intensive. This increased productivity allows jam manufacturers to meet the growing market demand and expand their business.
2. Improved Product Quality
The vacuum – sealing process ensures that the jam remains fresh and flavorful for a longer time. By removing the air from the jar, the machine reduces the risk of spoilage and extends the shelf – life of the product. Additionally, the precise cap – placement and sealing mechanisms result in a consistent and high – quality seal on every jar, enhancing the overall appearance and integrity of the product.
3. Cost – Savings
Although the initial investment in a fully automatic capping machine may be significant, it can lead to long – term cost – savings. By reducing the need for manual labor, the machine lowers labor costs. It also minimizes the risk of product loss due to improper sealing, which can save money in the long run. Moreover, the energy – efficient design of modern capping machines helps to reduce electricity consumption.
4. Hygiene and Safety
In the food industry, hygiene is of utmost importance. Fully automatic capping machines are designed to minimize human contact with the jars and caps, reducing the risk of contamination. The machines are made of materials that are easy to clean and sanitize, ensuring a hygienic production environment. Additionally, they are equipped with safety features such as emergency stop buttons and sensors to prevent accidents.
Maintenance and Troubleshooting
1. Regular Maintenance
To ensure the optimal performance of the fully automatic jam glass jar vacuum capping machine, regular maintenance is essential. This includes cleaning the machine after each use to remove any jam residues or debris. The moving parts should be lubricated regularly to prevent wear and tear. The vacuum pump and other components should be inspected periodically for any signs of damage or malfunction.
2. Troubleshooting
Despite proper maintenance, issues may still arise. Common problems include misaligned caps, inconsistent vacuum levels, or sealing failures. In case of misaligned caps, the cap – placement mechanism may need to be adjusted. If the vacuum level is inconsistent, the vacuum pump should be checked for leaks or blockages. Sealing failures can be caused by incorrect temperature or pressure settings, and these settings should be adjusted accordingly.
Conclusion
A fully automatic jam glass jar vacuum capping machine is an indispensable tool for jam manufacturers. Its advanced technology, high – speed operation, and numerous benefits make it a valuable investment. By understanding its working principles, benefits, and maintenance requirements, manufacturers can ensure the smooth and efficient operation of the machine, leading to high – quality jam products that meet the expectations of consumers.