في عالم تكنولوجيا التغليف ، ظهور سدادات المؤازرة ذات الرأس المزدوج قد رفع الشريط للدقة والأداء. إليكم سبب ترك الآلات التقليدية في الغبار.
تقدم السدادات المؤازرة ذات الرأس المزدوج مستوى دقة لا مثيل لها. يضمن النظام الذي يحركه المؤازرة تنفيذ كل عملية ختم بدقة دقيقة ، مما يؤدي إلى أختام لا تشوبها شائبة باستمرار. يعد هذا المستوى من الدقة أمرًا بالغ الأهمية في الصناعات التي تكون فيها تكامل المنتج ومراقبة الجودة أمرًا بالغ الأهمية.
التكوين ثنائي الرأس يعزز بشكل كبير الإنتاجية. من خلال العمل في وقت واحد ، يمكن لهذه السدادات التعامل مع مرتين عبء العمل في نفس مقدار الوقت مثل آلات الرؤوس الواحدة التقليدية. تترجم هذه الكفاءة المتزايدة إلى دورات إنتاج أقصر وإخراج أعلى.
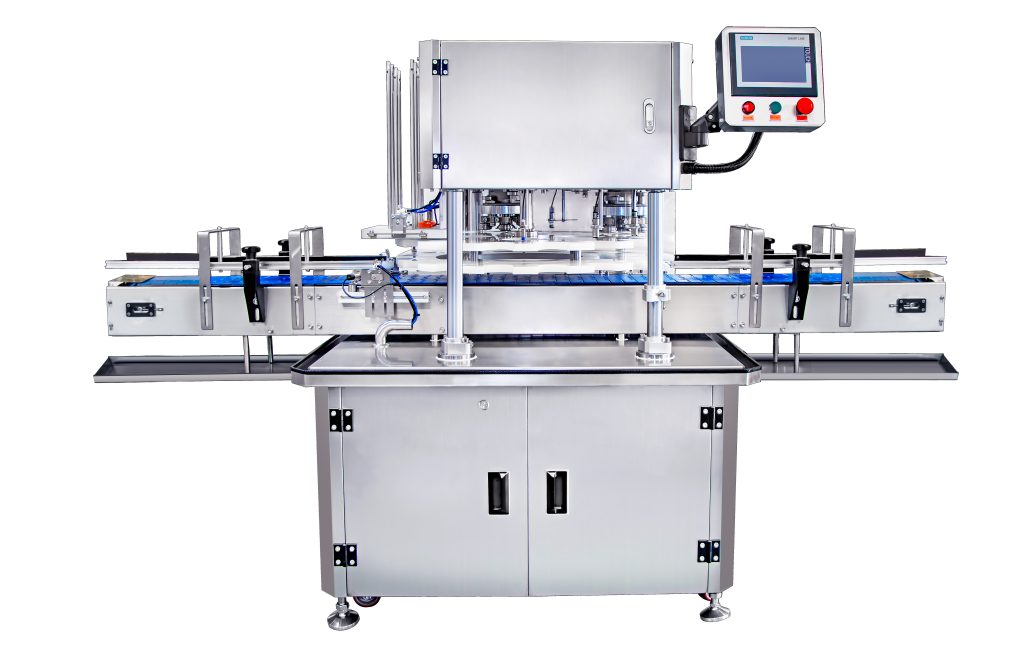
أنها توفر أيضا مرونة أكبر وقدرة على التكيف. يمكن برمجة السدادات المؤازرة ذات الرأس المزدوج بسهولة وتعديلها لاستيعاب أحجام وأشكال ومواد مختلفة للتغليف. هذا يجعلها مناسبة لمجموعة واسعة من المنتجات ومتطلبات الإنتاج.
أنظمة التحكم المتقدمة لهذه السدادات تسمح بدقة المعلمات مثل الضغط ودرجة الحرارة والسرعة. يمكّن ذلك المشغلين من تحسين عملية الختم لمواد وتطبيقات محددة ، وضمان أفضل النتائج الممكنة.
على النقيض من ذلك ، غالباً ما تكافح الآلات التقليدية لتتناسب مع السرعة والدقة ومرونة سدادات المؤازرة المزدوجة. قد تكون عرضة للأختام غير المتسقة ، والتشغيل الأبطأ ، والتكوين المحدود.
باختصار ، فإن الجمع بين الدقة المعززة ، وزيادة الإنتاجية ، والمرونة ، والتحكم المتقدم يجعل سدادات المؤازرة ذات الرأس المزدوج الخيار المتفوق لعمليات التغليف الحديثة. أنها تمثل قفزة إلى الأمام في التكنولوجيا التي تعيد تشكيل الصناعة ووضع معايير جديدة للجودة والكفاءة.